A new packaging line for insulation panels
September 11, 2023 7:27 pm
Steinbacher Dämmstoff GmbH in Austria has installed a new packaging line for PU insulation panels. A RoRoStretchPack solution has replaced two packaging lines for packaging multiple panel sizes. Improved 6-sided packaging and automation are the headlines behind installing the new packaging line.
Steinbacher searched for a fresh solution for packaging their PU insulation panels for some time. The primary reason is the need to enhance packaging quality. The Production Manager at Steinbacher in Erpfendorf, Markus Brandstätter, emphasised, “Securing waterproof packaging is a top priority for us. Our end-customers often store the panels outdoors at construction sites, and due to high demand, we can’t always store the panels indoors before shipping.” Markus elaborated, “Our previous packaging approach lacked waterproofing, which led to the potential issue of water getting trapped between the panels when stored outside.”
Previously, the standard-sized PU panels (1200×600 mm) were packed with a sleeve to create four-sided packaging for a bundle of panels. These bundles were then arranged on a pallet and wrapped using stretch wrap film. The larger panels were earlier packaged utilising heat shrink, but consistent problems emerged with the weldings. Consequently, neither of these packaging methods ensured complete waterproofing.
Six-sided packaging – sealed and waterproof
Markus Brandstätter says, “A few years ago, we came across RoRoStretchPack® produced by Tentoma”. RoRoStretchPack® is a horizontal packaging solution employing a tubular stretch hood film covering all six sides. Achieving sealed and waterproof packaging only requires welding the two ends of the film. Both packaging and sealing steps are integrated into a single process. This innovation was developed by Tentoma in Denmark, inspired by the established vertical stretch hood packaging technique commonly utilised for five-sided pallet packaging.
Markus explains,” After the initial assessment, we sent different sizes of product samples to Tentoma for test packaging. When the packaging samples returned to Austria, they were thoroughly tested regarding packaging quality, environmental impact, and logistics. We also investigated consumables, potential savings, and automation to evaluate the business case”.
Energy savings
Maximum energy efficiency and cost savings to improve sustainability are focus areas for Steinbacher. Markus Brandstätter says,” Previously 20-30 percent of the packaging used heat shrink. This is now replaced by RoRoStretchPack® packaging. By directly comparing our previous packaging solution and RoRoStretchPack® packaging, we have reduced energy consumption by about 50 percent on the packaging line”.
Film consumption is also an important parameter of both cost and sustainability. Steinbacher is monitoring the film consumption per pallet. Even though Steinbacher has gone from 4-sided to 6-sided packaging, they have reduced film per pallet by using RoRoStretchPack®. Markus adds, “Now that we have become familiar with the new packaging line, we will optimise the process to further film reductions.”
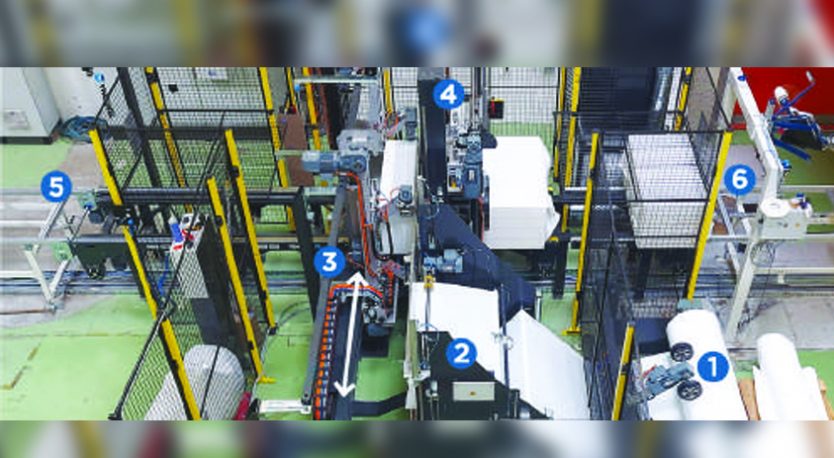
A structured project process
Markus Brandstätter states, “Summarising the project process went very well from the first contact till installation and commissioning. It was a structured process with good communication with Tentoma. We had fixed monthly meetings and later fixed weekly meetings when the FAT (Factory Acceptance Test) approached. Both the FAT and the installation were well planned and executed.”
In connection with the installation, Tentoma trained three employees from Steinbacher as key users on the new packaging line. He concludes, “Our employees felt confident with the new packaging line after the introduction. We are satisfied with the capacity and the packaging quality of the new RoRoStretchPack® packaging solution.”
Benefits for Steinbacher Dämmstoff GmbH
· 6-sided packaging and waterproofness
· Improved and uniform satisfied quality
· Removed heat shrink from the packaging
· 50% energy savings on the packaging line
· Automation and reduced number of processes in the packaging line.
View of Steinbacher’s new inline RoRoStretchPack® packaging line.
· The film stand (FS) contains up to 12 km of film, which reduces the number of film shifts.
· The film unit (FU) welds the front end of the tubular film to create a hood.
· The gripper unit (GU) stretches and moves the film to the packaging lane. The film is rolled off the GU while the panels are packed.
· The back sealing unit (BU) seals the 6-sided packaging.
· The in-feed conveyor receives the panels directly from the production line.
· The output conveyor transports the packed panels to a labelling machine and a palletising system.
Production manager, Mr Markus Brandstätter: ”We are satisfied with the capacity and the packaging quality of the new RoRoStretchPack® packaging solution”.
For more information, visit: www.tentoma.com
Cookie Consent
We use cookies to personalize your experience. By continuing to visit this website you agree to our Terms & Conditions, Privacy Policy and Cookie Policy.